Benefits of offsite manufacturing in housing
- Mehdi Shahparvari
- Aug 6, 2021
- 3 min read
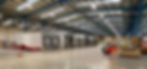
There are different terminologies used for industrialised construction in the literature – such as; for example, off-site production (OSP), off-site manufacturing (OSM), prefab, modern methods of construction (MMC), industrialised construction, and modular construction (Modular). A very simple model was introduced to differentiate the level of industrialisation of construction works as shown in Figure 1.

Fig1. The adaptation of industrialised housing hierarchy
Traditional construction is fully craft-based construction using workmanship in which all of the processes happen onsite and involves in situ manufacturing and installation of prefabricated elements such as doors, windows, pipes, bricks, tiles, etc. On-site prefabrication is the assembly of building components on-site which are then moved into position (components such as timber framing, handmade roof trusses and façade units). As opposed to on-site prefabrication, the off-site manufacturing is assembly of building components and then transporting them to site and assembling in place such as air conditioning units or roof trusses. Pods are pre-assembled units such as toilets or bathrooms manufactured off-site and then transported to site where connect them to other building components. Complete modular encompasses fully finished units that form the complete structure and form a building. However, manufactured housing has often been neglected – as construction industry has a tendency of being sluggish to adopt and proceed with emerging technologies.
Off-site technologies have several potentials to reduce negative environment impact, increase re-use of recycling materials, eliminating waste, minimising rework, reducing cost, optimise the performance of projects and the quality of products. There are great advantages associated with manufactured housing over traditional construction method, such as higher precision, reduction of lead time, improving delivery , more energy efficient to operate and cost efficient. This result in shortening the completion process of building with higher quality. One of the striking benefits of fully automated off-site manufacturing is elimination of human errors – preventing rework occurrence, as well as the adversity of site condition (i.e., weather, etc.) in construction projects . These aspects can significantly reduce rework and consequently prevent projects from cost and schedule overrun. It has been found that manufactured housing can save up to 20% of time compared to on-site construction There are other indirect benefits associated with off-site prefabrication due to reduced site preliminary costs, reduced site congestion and earlier income generation for clients. It has been shown that off-site prefabrication can also reduce safety risks around 35% due to less site congestion and removing operatives from a dangerous site environment to a controlled factory environment with better working conditions.
A survey conducted with the top 100 UK house builders stated motivation is the most critical factor applying off-site manufacturing to attain a high quality product. Another study found that off-site prefabrication could reduce the need for many trades that are in short supply, thus, can eliminate necessary rework in different stage of processes. However, lack of technology awareness, cultural perception, high initial investment costs, lack of business process model, incompatibility and inflexibility of design are identified as the most challenging barriers for off-site manufactured housing. For instance, in Hong Kong the Provisional Construction Industry Coordination Board has noted that high initial investment remains a significant obstacle to the adaptation of off-site prefabrication techniques.
The inflexibility of design was a major issue for off-site prefabrication due to the requirement of an early design freeze. The findings also suggested that the main barrier for off-site prefabrication is considered cost, design, logistic and transportation also have been taken into the account as a major impediments to the adaptation of off-site prefabrication.
The idea of Digital Twin
Digital Twin (DT) incorporated with offsite manufacturing technologies can improve the quality of offsite manufacturing products, reducing unintended errors and improving the quality of buildings throughout the lifecycle. A fully robotically automated fabrication process in offsite manufacturing with application of DT - can enable digitised visualisation of a virtual replica of a physical object in factory floor to improve the quality issues and keep monitoring product’s maintenance live.
Further Readings
Gann, D.M., (1996). Construction as a manufacturing process? Similarities and differences between industrialized housing and car production in Japan. Construction Management & Economics, 14(5), pp.437-450. https://doi.org/ 10.1080/014461996373304
Gibb, A. and Isack, F., 2003. Re-engineering through pre-assembly: client expectations and drivers. Building Research & Information https://doi.org/10.1080/09613210302000.
Gibb, A.G., (1999). Off-site fabrication: prefabrication, pre-assembly and modularisation.
Hampson, K.D. and Brandon, P., (2004). Construction 2020-A vision for Australia's property and construction industry. CRC
Latham, S.M., (1994). Constructing the team.
Nadim, W. and Goulding, J.S., 2010. Offsite production in the UK: the way forward? A UK construction industry perspective. Construction innovation, 10(2), pp.181-202. https://doi.org/10.1108/14714171011037183
Steinhardt, D.A., Manley, K. and Miller, W., (2013). Profiling the nature and context of the Australian prefabricated housing industry.
Steinhardt, D.A., Manley, K. and Miller, W., (2014). Predicting Australian builders’ intentions to use prefabrication.
Steinhardt, Dale A., Karen Manley, and Wendy Miller., (2014). "What’s driving the uptake of prefabricated housing in Australia?"